7. Topic 4, Case Study 4, Fabrikam inc.
Fabrikam, Inc. Is a discrete manufacturer of outdoor patio furniture. The company originated as a sole owner working from a home garage, then moved into a commercial storage space, and later into a full manufacturing facility. The company operates as two operating legal entities, one in the United States and the other in Mexico.
As the company grew, the existing software systems failed to grow with it. This meant that financial reporting was managed in an outdated accounting system; raw materials planning, production, and inventory control were managed in another system; and cost calculations were tracked in multiple spreadsheets managed by analysts.
Current environment
The Fabrikam. inc. engineering team uses a third-party computer-aided design (CAD) system for drawings. These drawings are later introduced into one or more companies for sale. A customer service center handles complaint calls and places orders for distributors.
The current system landscape creates a lack of controls and visibility across the systems, leading to overages of some raw materials, shortages on others, and large quantities of scrap. Heavy production volume provides little to no room for system downtime. The staff manually creates production orders, which leads to double work for system entry later. This delay has a ripple effect into the materials planning.
The company currently sources teakwood from India, making it a more expensive and high-end material. Cedar and redwood are both sourced from the Western US. Truck driver shortages across the nation have caused shipping costs to rise sharply.
Fabrikam, Inc. recently decided to expand into the gas firepit market. All products are currently being prototyped. The company decides that the firepit prototype should be initially available only in the United States. The firepits will be manufactured only in Nevada and Arizona. The firepits are produced as prototyping: this production line operates only on Mondays.
Fabrikam, Inc. has purchased new manufacturing equipment for the firepit metal fabrication. This purchase includes a warranty, which requires that the company perform routine maintenance. Fabrikam, inc. elects to complete the maintenance in house on a quarterly schedule and maintain appropriate records for warranty purposes. The metal fabrication equipment consists of three separate machines used in a single production process.
Fabrikam. Inc. made the decision to move to Dynamics 365 Supply Chain Management.
Application and environment
• Fabrikam, inc. must move systems and processing to software as a service (SaaS) whenever possible because the company does not have enough IT staff to support hardware.
Inventory and costing
• Finished goods fall into three categories:
• Wood furniture (teak, cedar, redwood) o Outdoor heating (firepits. gas heaters)
• Each outdoor heating item with slight variations, such as a chrome or steel finish, must have a unique item number, o Repair parts (nuts and bolts, ignitors. and other parts)
• The system must account for the fact that Fabrikam. inc. must take legal ownership of teakwood at the time of shipment, not at the time of receipt into the warehouse.
• The company must accrue for the costs of the teakwood materials as soon as the company takes ownership. The company takes ownership at the time of shipment, which is posted prior to physical receipt at the warehouse.
Engineering
• Engineers who specialize in gas consumer goods will design the firepits and ate the only users with authority to release the products for sale.
• Engineering must notify customer service of any open orders that may contain a released product version that may be discontinued or delayed.
• The change request workflow must route to the engineer.
Production
• The raw material and subcomponent goods for the firepit must be managed by the engineer. This means the engineer must oversee any new items, material changes, address problems, and so on.
• The metal fabrication equipment must be tracked at the locations where the firepits are produced.
• The production team must operate on an all-day/everyday model, with each team operating in a 12-hour shift. This is a recent change to keep up with high demand for products, as well as for planning a new product line.
• Raw material and subcomponent items for the firepit prototype must not be available for use until engineering is ready for the prototype product release.
• Due to the production staff schedule, all equipment must be planned according to the staffing.
• Maintenance for each of the three pieces of machinery must be scheduled at the same time so that only the local maintenance technician works on the equipment.
• When the firepits are ready for the test market they must made be available for sale.
• The United States operating company must review any engineering products before they are available for sales or production orders,
• The engineering team must release the engineering product into the United States operating company,
• The engineering BOM lines must not be removed by the United States operating company. Application and environment
• The operations manager is concerned that system downtime is so frequent that It is impacting efficiency due to the all-day/everyday production operation model.
Inventory and costing
• Fabrikam, inc. marketing campaigns in the desert states of Arizona- Nevada, and New Mexico have led to an increased demand for teakwood furniture to endure weather elements. Supply and demand for this wood lowered expected margins with increased shipping costs and price increases from the vendors.
• User1 reports that the inventory value of the teakwood is not on the financial reports, even though ownership of the product begins at the port of shipment,
• Upon receipt into the physical warehouse, User2 reports that the warehouse workers received less teakwood than the ordered amount on the purchase order.
Engineering and production
• As the firepits are produced and feedback received from the test market, records must be maintained of each revision to the firepit design.
• Firepits must have attributes associated with them to specify the type of gas line that is available for the firepit such as natural gas or propane.
• Customer service is receiving calls that the firepit ignition switch does not always work as expected. This issue was reported through an engineering change request.
• User3 reports resource issues on the production shop floor due to system maintenance issues and other delays. The company does not want User3 or the other workers to stop production.
• User4 reports that a bolt needed for cedar wood furniture is out of stock. A temporary substitution bolt was identified prior to starting the production order.
• User5 reports that a hinge for redwood furniture will be discontinued at the end of the year. Production must reflect an updated part.
• A large order was placed for 1,500 pieces of teakwood furniture and production orders must start as soon as possible.
• Users reports the following:
• Only 100 pieces of furniture can be produced on the night shift due to resourcing. Enough raw materials are on hand to complete 100 pieces, but not enough to produce all 1.500 pieces.
• The production floor is organized into dedicated production lines, each with their own warehouse. The warehouse workers must pick the raw materials to the correct warehouse location.
HOTSPOT
You need to meet the needs for the large teakwood furniture order.
What must you configure? To answer, select the appropriate options in the answer area. NOTE: Each correct selection is worth one point.
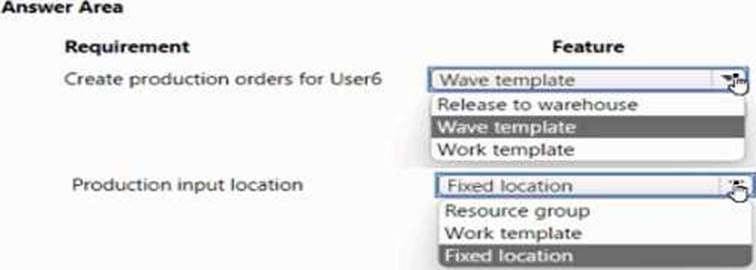
LEAVE A COMMENT